Workwear is designed to protect the worker against certain risks found in the workplace, like physical injuries and electric shocks. Given the risks, there are regulations such as the Personal Protective Equipment Regulation that require workwear to meet high safety standards.
In this guide, we cover regulations and their requirements relevant to workwear, which cover requirements such as documentation, labelling, and testing.
Content Overview
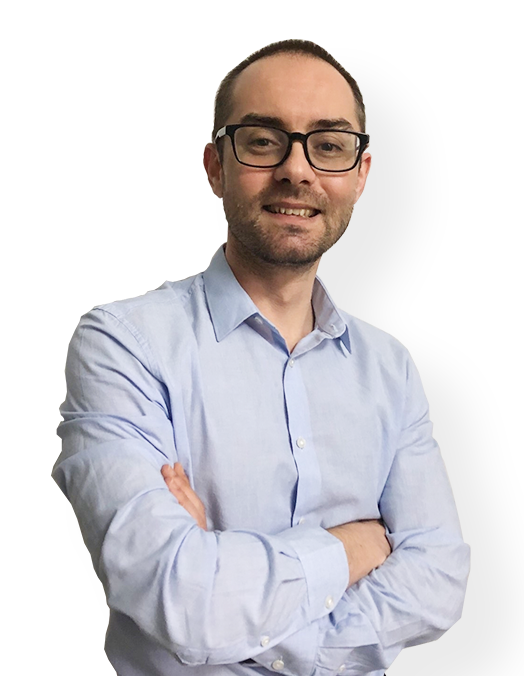
FREE CONSULTATION CALL (US, EU & UK)
- Request a free 30-minute call with Ivan Malloci to learn how we can help you with:
- Find product requirements
- Certification and labeling
- Lab testing
Personal Protective Equipment (PPE) Regulation
The Personal Protective Equipment Regulation covers products that can be held or worn, and that are designed to protect the user from one or more risks to the person’s health or safety. Such products include workwear.
The regulation contains various types of requirements which include conformity assessment procedures, documentation, labelling, and testing. Some requirements differ according to the product’s risk category.
PPE categories
PPE products can be classified into one of the following categories depending on the risk it is designed to protect the user against:
- Category I PPE (e.g. Light anti-scalping helmets)
- Category II PPE (e.g. Welding goggles)
- Category III PPE (e.g. Protective gloves against harmful biological agents)
The higher the category, the more serious the risks the equipment is meant to protect against.
Harmonised standards
Harmonised standards when applied ensure that the product conforms to the essential safety requirements of the regulation. The regulation contains many harmonised standards for workwear. Here we list some examples.
Title | Description |
EN 16689 | This standard covers protective clothing for firefighters. These are products that protect the wearer for certain rescue scenarios. It contains performance requirements, test methods and marking and information to be supplied by the manufacturer. |
EN 352-1 | This standard covers hearing protectors (ear muffs) and contains design, performance, and labelling requirements for such products. |
EN 388 | This standard covers protective gloves. It contains safety requirements, test methods, and labelling requirements. |
EN 397 | This standard covers industrial safety helmets. It contains physical and performance, test methods and labelling requirements for covered products. |
Documentation
Here we list the main documents referred to in the regulation.
Title | Description |
Declaration of Conformity | This document is issued by the manufacturer. It should contain information about the product, a declaration that the product conforms with the relevant regulation(s), applied standards, and supporting information. |
Technical documentation | The technical documentation refers to a set of documents listed in Annex III of the regulation. The documents serve as evidence that the product conforms to the regulation requirements. |
Instructions | The document is required to accompany the product and it should contains instructions and safety information related to the product. |
Labelling requirements
Here we list the main labelling requirements contained in the regulation.
Title | Description |
CE marking | ![]() The CE marking indicates that the product conforms to the PPE Regulation. |
Pictograms or other markings indicating the risk | These are labelling information that indicates the risks which the product is designed to protect against. Such information should accompany the product and may be presented after CE marking. |
Notified body identification number | Category III PPE products involve a notified body. The identification number of the notified body should follow the CE marking. |
Traceability information | This refers to information that would enable consumers and the authorities to retrieve identifying information about the product and contact details of the manufacturer. |
Textile Labelling and Fibre Composition Regulation
The Textile Labelling and Fibre Composition Regulation contains labelling requirements for products made out of textile material, including workwear. It requires the label of the textile products to contain the name of the textile fibres used and the fibre composition.
Additionally, if the product contains non-textile parts of animal origin (e.g. leather), it must contain the statement: “Contains non-textile parts of animal origin”.
Biocidal Products Regulation
The Biocidal Products Regulation covers biocidal products and products treated with biocidal products. In this article, we focus on treated articles as they may include workwear.
For example, workwear that is treated such that it is anti-fouling would be covered. Such treated articles would be affected by the regulation’s requirements, including those relating to:
- Substance restriction
- Labelling
- Documentation
Substance restrictions
The regulation requires treated articles to only use biocidal products with approved active substances. Additionally, some approved substances come with conditions or restrictions.
Documentation requirements
The regulation requires suppliers to provide information to consumers within 45 days of receiving a request to provide information about the treated article.
Labelling requirements
The regulation requires a product to come with labelling information about the biocidal products used and the biocidal properties of the product where:
a. Claims are made that the product contains biocidal properties
b. The biocidal product(s) used to treat the product requires labelling information to be provided
The label must include information such as:
- The product’s biocidal property
- Instructions for use
- Precautionary information
REACH
The REACH Regulation contains substance restriction requirements for articles, including workwear. Lab testing is generally necessary to assess whether the product contains substances restricted by Annex XVII or substances of very high concern (SVHCs).
Restricted substances (Annex XVII)
Here are some restricted substances that may be found in workwear:
a. Tris (2,3 dibromopropyl) phosphate – Prohibited for use in textile materials intended to be in contact with skin
b. Azocolourants and Azodyes – Aromatic amines released must not exceed 30 mg/kg (0.003 % by weight) for textile and leather articles
c. Tris(aziridinyl)phosphinoxide – Must not be used in textile articles intended to come into contact with the skin
d. Formaldehyde – The concentration of formaldehyde released must not exceed 0.080 mg/m3 for articles other than furniture and wood-based articles
SVHC
If a product contains SVHCs above concentration levels of 0.1% you must:
a. Notify the ECHA of the substances, via the SCIP database
b. Communication of information relating to identified substances down the supply chain
Here are some examples of SVHC that may be relevant for workwear, for example because they can be found in textile products:
- Bumetrizole
- Bis(4-chlorophenyl) sulphone
Lab Testing
Lab testing is necessary to verify whether the workwear conforms to the safety requirements contained in the applicable regulations. Test reports retrieved from testing companies can be used to support the product’s conformity. Here we list the regulations mentioned in this article and examples of their testing requirements.
Regulation | Lab testing |
PPE Regulation | This regulation contains a number of harmonised standards that apply to different types of workwear. Standards may contain testing methods which include:
|
Biocidal Products Regulation | The Biocidal Product Regulation contains substance restrictions.
To confirm whether your product is compliant with the regulation, testing may be necessary (e.g. testing for the presence of restricted substances). |
REACH | Products should be tested to ensure they do not contain restricted substances in concentrations exceeding allowable limits.
For example, textile components of wearing apparel that come into contact with human skin should be tested to ensure they do not contain Tris (2,3 dibromopropyl) phosphate. |
Workwear testing companies
To satisfy the testing requirements for the regulations that are listed above, a lab testing company should be approached. Here are some lab testing companies that offer testing services for workwear:
- QIMA
- Intertek
- Bureau Veritas
Additional Requirements
In addition to the requirements mentioned above, there are other regulations that could be relevant to your workwear.
Regulation | Description |
General Product Safety Regulation | The General Product Safety Regulation requires the manufacturer to ensure their product is safe. It covers safety aspects that are not already covered by other regulations (e.g. the PPE Regulation).
The regulation contains labelling, documentation, and other requirements. It may require lab testing to conform to its requirements. |
Persistent Organic Pollutant Regulation | The Persistent Organic Pollutant Regulation contains substance restrictions, including for the use of PFOS in textiles and other products.
You should consult a lab testing company to confirm whether testing would be needed under this regulation for your product. |
Recommended articles
Very helpful article about PPE! Thank You also for guides explaining exactly procedures of testing.
Hi Kons,
We will add more info on the testing process in the future.