Smoke defectors imported or manufactured for sale in the United States must comply with various safety standards and labelling requirements. In this guide, we take a closer look at UL standards, NRTL Approvals, 47 CFR Part 15, and other compliance requirements relevant to smoke detectors in the US.
Content Overview
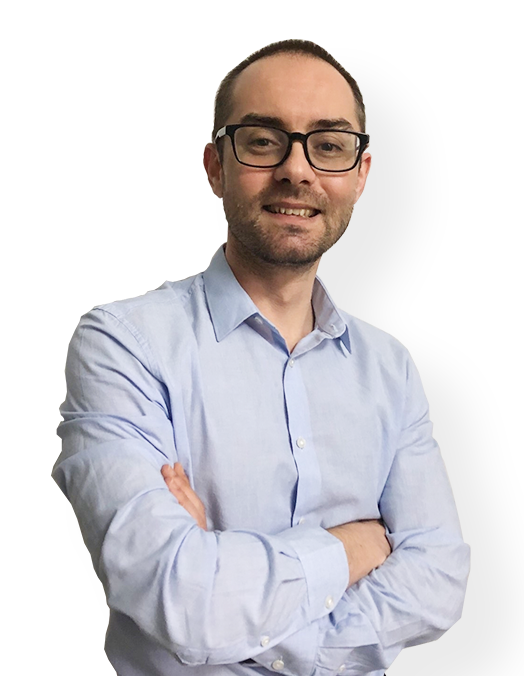
FREE CONSULTATION CALL (US, EU & UK)
- Request a free 30-minute call with Ivan Malloci to learn how we can help you with:
- Find product requirements
- Certification and labeling
- Lab testing
UL Standards
There are several UL standards that cover smoke alarms, smoke detectors, and similar products. Some standards are incorporated by reference (e.g. under 24 CFR Part 3280), and thus are mandatory.
Other standards are not incorporated by reference into any regulation, meaning they are voluntary in theory. In practice, however, you have to ensure product safety, and thus, you need to make sure that your product complies with the requirements of relevant standards. Also, marketplaces and distributors often refuse to list or purchase products that do not comply with UL or other standards.
Here we list some examples of standards for different types of smoke detectors and related products. Note that other standards may exist.
Standard | Description |
UL 217 – Smoke Alarms | The standard sets requirements for:
a. Electrical smoke alarms for single and multiple stations that are meant to protect open areas in indoor locations b. Portable travel smoke alarms 24 CFR Part 3280 incorporates UL 217 by reference. |
UL 268 – Smoke Detectors for Fire Alarm Systems | This standard establishes requirements for smoke detectors and accessories for use in indoor locations per the NFPA 72 code in the United States.
It covers: a. Detectors meant to protect open areas b. Detectors meant to control releasing devices (e.g. electromagnetic door holders) 24 CFR Part 3280 incorporates UL 268 by reference. |
UL 268A – Smoke Detectors for Duct Application | This standard applies to air duct smoke detectors that are either intended for indoor use or are mounted in a housing. |
UL 228 – Door Closers-Holders, With or Without Integral Smoke Detectors | This standard sets requirements that apply to:
a. Swinging door closers that are equipped with inbuilt integral smoke detectors b. Electromagnetic door holder units used with a fire detector |
UL 1730 – Smoke Detector Monitors and Accessories for Individual Living Units of Multifamily Residences and Hotel/Motel Rooms | This standard sets requirements for electrically-operated smoke detector monitors meant to be used indoors per:
|
UL 2034 – Single and Multiple Station Carbon Monoxide Alarms | This standard sets requirements for electrically-operated station carbon monoxide alarms that are meant to protect people in indoor places such as:
It does not, however, cover smoke alarms covered by UL 217 and UL 268, fire alarms covered by UL 539, and heat alarms covered by UL 521. 24 CFR Part 3280 incorporates this standard by reference. |
NRTL Approval
As explained in the Type of Products Requiring NRTL Approval page published by the Occupational Safety and Health Administration (OSHA), there are 39 product types that require approval by a Nationally Recognized Testing Laboratory (NRTL). This includes automatic fire detection systems and equipment.
While NRTL approval is generally not compulsory for manufacturers, if you want to sell these products to employers, you must get them approved by an NRTL. The reason is that employers must follow OSHA requirements. Thus, they would not buy your fire detection systems, unles they are NRTL approved.
Standards
Covered products should comply with the appropriate standards listed on OSHA’s website. Here are several examples of listed standards relevant to smoke detectors:
UL 217 – Single and Multiple Station Smoke Detectors
UL 228 – Door Closers-Holders, and Integral Smoke Detectors
UL 268 – Smoke Detectors for Fire Protective Signalling Systems
UL 268A – Smoke Detectors for Duct Application
UL 555S – Leakage Rated Dampers for Use in Smoke Control Systems
UL 1730 – Smoke Detector Monitors and Accessories for Individual Living Units of Multifamily Residences and Hotel/Motel Rooms
FM 3230 – Smoke Actuated Detectors for Automatic Fire Alarm Signaling
OSHA states on its website that fire detection systems should also adhere to the requirements set in 29 CFR Part 1910.164, which sets requirements for employers.
Certification
Manufacturers who intend to sell their smoke detectors to companies subject to OSHA regulations should get their products tested and certified by an NRTL. When an NRTL certifies a product, the Laboratory authorizes the manufacturer to affix its registered certification mark onto the product.
NRTL Mark
An NRTL mark signifies that the product has been tested and certified by an NRTL. This in turn means that the product comply with the requirements of the appropriate standards.
Note that the mark will be different, according to the NRTL of your choice.
NRTLs
Only NRTLs can test and certify your product before providing you with a registered certification mark. Here are several examples of NRTLs listed on OSHA’s website:
- Bureau Veritas Consumer Products Services, Inc. (BVCPS)
- Intertek Testing Services NA, Inc. (ITSNA)
- SGS North America, Inc.
- TÜV SÜD Product Services GmbH
- UL LLC
24 CFR Part 3280 – Manufactured Home Construction and Safety Standards
24 CFR Part 3280 sets requirements and safety standards for manufactured homes, which the regulation defines as a structure meant for living that has a permanent chassis.
24 CFR Part 3280.209 specifically covers smoke alarm requirements, and it sets requirements such as the following:
a. Installation requirements (e.g. at least one smoke alarm should be installed in each bedroom)
b. Mounting requirements (e.g. smoke alarms should undergo installation on either the ceiling at least 4 inches from the walls, or a wall at most 4 inches below the ceiling)
c. Power requirements (e.g smoke alarms should use a battery with a 10-year lifespan)
d. Notification requirements (e.g. manufacturers of smoke alarms should provide a visible and tactile notification appliance with their product)
e. Labeling and instruction requirements (e.g. smoke alarms should bear a label stating conformity with the relevant UL standards)
f. Testing requirements (e.g. smoke alarms should undergo a dielectric test per 24 CFR Part 3280.810(a), and operational tests)
Instructions
The regulation mandates manufacturers to provide installers with written instructions for inspecting and testing the alarm when installing the home. Additionally, they need to provide homeowners with information such as:
- Operation of the smoke alarm
- Method and frequency of testing of the smoke alarm
- Proper maintenance of the smoke alarm
Labeling requirements
The regulation mandates smoke alarms to bear a label indicating compliance with the requirements of standards incorporated by reference – that is, either UL 217 or ANSI/UL 268. Combined smoke and carbon monoxide alarms should bear a label indicating compliance with both UL 217 and ANSI/UL 2034.
Testing requirements
The regulation requires smoke alarms to undergo several tests, such as:
- Dielectric test specified in 24 CFR Part 3280.810(a)
- Operation test.
NFPA Codes
NFPA codes generally provide guidelines and requirements on electrical, fire, and life safety. Here we list two examples of NFPA codes that may be relevant to smoke detectors. Note that other relevant NFPA codes may exist.
Standard | Description |
NFPA 72 – National Fire Alarm and Signaling Code | NFPA 72 provides fire alarm and detection, signaling, and emergency communications requirements. It also sets mass notification system requirements for a variety of threats and emergencies. |
NFPA 101 – Life Safety Code | NFPA 101 sets life safety requirements for both existing and new structures. It also provides procedures to protect people based on features such as building construction and occupancy that can lessen the effects of flame and fire-related risks. |
47 CFR Part 15 – Radio Frequency Devices
47 CFR Part 15 regulates electrical and electronic devices that emit radiofrequency within the 9 kHz to 3000 GHz frequency range, including smoke detectors. Covered products are classified into intentional radiators and unintentional radiators.
Importers and manufacturers should ensure that:
- Their product undergoes the relevant authorization procedure
- They provide relevant documentation
- They properly label their product
- They get their product tested
Intentional radiators
Intentional radiators are devices that emit and generate radiofrequency energy via induction or radiation, such as smoke detectors with Wi-Fi or Bluetooth capabilities.
Here we list the key requirements:
a. The product should undergo the certification authorization procedure
b. The product should comply with relevant standards (e.g.ANSI C63.10-2013)
c. The product should comply with technical requirements (e.g. with good engineering design, emitted radiation should not exceed acceptable levels)
d. Importers and manufacturers should provide a technical report (containing, for example, the applicant’s name, FCC identifier, and instructions for installation)
e. Importers and manufacturers should properly label the product (e.g. with a compliance information statement)
f. The product should undergo product testing by an FCC-recognized accredited testing lab
Unintentional radiators
Unintentional radiators are devices that are not designed to emit radiofrequency energy via induction or radiation and send signals by connective wiring within the device. Smoke detectors that do not have Wi-Fi, Bluetooth, or similar capabilities are unintentional radiators.
Here we list the key requirements for unintentional radiators:
a. The product should undergo the Supplier’s Declaration of Conformity (SDoC) authorization procedure
b. The product should comply with radiated emission levels, relevant standards, and requirements
c. Importers or manufacturers should provide technical documentation and an SDoC compliance statement
d. Importers or manufacturers should properly label the product (e.g. with the product’s trade name and model number)
e. The product should undergo testing
Lab Testing
You generally should get your product tested to prove it complies with the requirements and relevant standards. Some regulations (e.g. 47 CFR Part 15) mandate testing and the subsequent provision of a test report to prove compliance. Even when other regulations do not require your product to undergo testing, you still should have your product tested to make sure it is safe to use and can protect consumers.
If your product passes testing, the lab issues you a test report indicating that your product complies with the relevant requirements.
Regulation | Lab testing |
UL standards | Smoke detectors should generally undergo testing to ensure they operate as intended. For example, heat detectors incorporated into smoke detectors should undergo fire tests. |
NRTL Approval | Smoke detectors should undergo necessary testing for NRTL approval. For example, smoke detectors that are incorporated with combination door closers and holders should undergo fire tests. |
24 CFR Part 3280 | 24 CFR Part 3280.209 sets requirements for smoke alarms, and mandates, for example, that smoke alarms undergo the dielectric test described in 24 CFR Part 3280.810(a) to ensure the product functions as intended. |
47 CFR Part 15 – Radio Frequency Devices | Intentional radiators should undergo testing to the methods specified in the standards. ANSI C63.10 is an example of one such standard. This testing requirement would apply to smoke detectors with WiFi or Bluetooth capabilities.
Unintentional radiators should undergo testing using the procedure specified in ANSI C63.4-2014. |
Smoke detector testing companies
Here are several companies that claim to test smoke detectors to any of the regulations listed in this guide:
- Intertek
- UL Solutions
- Bureau Veritas
- SGS
Additional Requirements
Here is a list of other regulations that may be relevant to smoke detectors.
Regulation | Description |
Hazardous Materials Regulations (HMR) | These regulations set requirements for the transportation of hazardous materials, including lithium batteries and other type of batteries. Smoke detectors may use covered batteries, and thus need to comply with the requirements regarding:
|
California Proposition 65 | The components of smoke detectors may be manufactured with materials containing restricted substances listed on the California Proposition 65 List. For instance, the casing may contain phthalates, and the battery terminal connectors may contain lead.
Therefore, smoke detectors should undergo testing to ensure that they do not contain restricted substances above the permitted limits. |
Country of origin | Smoke detectors, like most products, need to bear a country of origin marking.
For example, if the product was made entirely in China, then the marking should read “Made in China”. |
Recommended articles