Are you an importer or a manufacturer looking to test your product? Whether you need to identify the chemical composition of your product or you want to assess if your product meets the relevant safety requirements, ‘laboratory testing’ should be considered.
That being said, lab testing is not necessarily a “one and done” thing. For starters, you can expect that you will need to re-arrange testing if you ever change materials, components, make design changes, or manufacturer. It is also necessary to re-test products as standards are amended, and new standards are implemented.
However, some regulations require that you go one step further and implement a periodic lab testing program – even without any such changes.
This article presents information relating to how frequently lab testing should be done. In addressing the question, we compare several US and EU product regulations. This includes the CPSIA and FCC 47 CFR Part 15 in the US, and the Toy Safety and the EMC Directive in the EU.
Content Overview
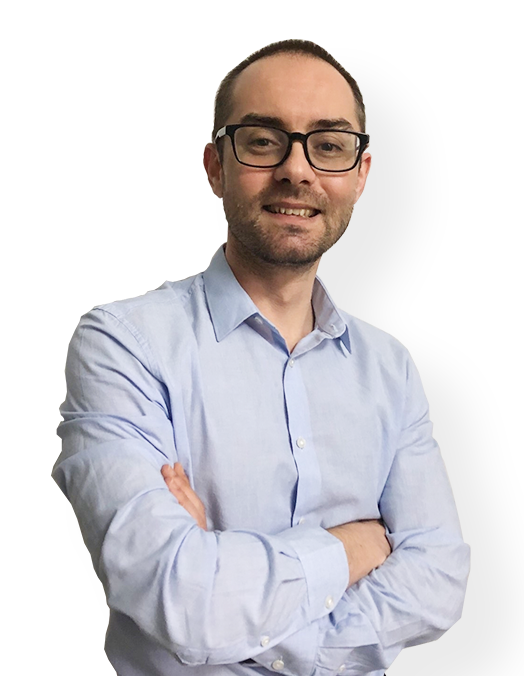
FREE CONSULTATION CALL (US, EU & UK)
- Request a free 30-minute call with Ivan Malloci to learn how we can help you with:
- Find product requirements
- Certification and labeling
- Lab testing
What is laboratory testing?
‘Laboratory testing’, also referred to as ‘product testing’ in the context of importing or manufacturing consumer products, entails testing a product against a specific standard or regulatory requirement in a controlled environment (e.g. a laboratory).
Here are some examples of different types of tests:
- Mechanical and physical properties testing
- Chemicals and heavy metals testing
- Flammability testing
- Electrical safety testing
- EMC testing
The lab may need to be an “accredited” or “accepted” third-party lab as, for certain regulated products such as children’s products in the US, designated labs have to be engaged. In other cases, any lab can be used.
When should a product be lab tested?
Products can be tested during the design and pre-production stage to ensure that the manufacturer is able to comply with the relevant standards and regulations’ requirements.
Pre-production testing: Verify product safety (e.g. mechanical safety and electrical safety), verify material compliance with substance regulations
Batch sample testing: Verify that the final product is fully compliant (not only samples)
Another stage of product testing might occur during production to ensure that the finished or semi-finished product (e.g. batch sample) meets relevant specifications. However, this is quite rare.
How often should I be testing my products?
The answer to this question depends on both the complexity of the product and the testing required by relevant regulations. For instance, some regulations might require testing every production batch.
Additionally, certain regulated regulations might require periodic testing or material change testing. The latter would require the regulated product to be tested a second time when changes are made to the product that could affect its ability to comply with the relevant standards and regulations.
Finally, there is always the possibility that a sample would fail to meet the required product specifications and would need to be re-submitted until it passes. Note that this might require changes to the design, components, or materials.
Can I ignore re-testing if there is no such requirement for a product?
Many product regulations don’t explicitly state how often and under what conditions a certain product should be re-tested. Instead, it’s up to the importer or manufacturer to determine what is reasonable in terms of testing frequency.
For obvious reasons, you may need to re-arrange lab testing under these conditions:
1. Material or component change
2. Design change
3. New manufacturer or production facility
4. New or amended product standards
5. New or amended substance limitations
6. New risks presented by marketed products
But, what do you do in a situation in which none of the above applies? No product or manufacturing process is static. Manufacturing defects and material contamination can render a product non-compliant even if nothing has changed.
As such, it is in your interest as a brand or manufacturer to implement some sort of periodic testing plan – if only for the sake of monitoring. Keep in mind that you are liable for your products, and can face a recall, with or without an explicitly written periodic testing requirement.
CPSIA (US)
In 2008, the Consumer Product Safety Improvement Act (CPSIA) amended and enhanced the CPSA and other CPSC statutes, aiming at ensuring safety for products intended for 12-year-old children, or younger children.
The CPSIA generally requires that children’s products comply with all applicable safety rules and undergo frequent mandatory testing to prove compliance by a CPSC-accepted accredited laboratory.
There are generally three types of testing for children’s products:
Initial certification testing
Your product would be required to be tested by a CPSC-accepted laboratory and based on the result issue a Children’s Product Certificate (CPC).
For some importers and manufacturers, the mandatory testing would stop here, especially for limited production runs and where no material changes are needed within each production run.
Material change testing
If there are material changes to the product (e.g., a new part is added to the toy), then the addition to the product or the whole product would have to be tested, and a new CPC should be issued.
Periodic testing
Additionally, if there are subsequent production runs, even if no material changes are made, periodic testing would be needed. The issuer of the CPC is responsible for periodic testing, and the CPSC requires the importer or manufacturer responsible to develop a written plan to ensure that such products are tested periodically.
‘Periodic testing’ plans
The CPSC has named three types of ‘periodic testing’ plans for products that undergo multiple production runs:
a. Periodic testing plan: the product must be tested at least once a year at a minimum, even if there are multiple production runs during the period
b. Production testing plan: the product must be tested at least once every two years, even if there are multiple production runs during the period
c. A plan that involves the use of a testing laboratory ISO/IEC 17025-accredited. In this case, a product must be tested at least once every three years, even if there are multiple production runs during the period
ISO/IEC 17025 accredited labs
These labs are approached by manufacturers opting for the three-year periodic plan in point c above.
Information obtained from testing conducted by an ISO/IEC 17025-accredited testing lab may be used to determine the appropriate testing interval to ensure a high degree of assurance that untested children’s products manufactured during the testing interval are in compliance with the applicable rules.
When to apply each CPSIA periodic testing plan?
According to the CPSC, periodic testing should be conducted often enough to demonstrate a high degree of assurance that the continuing production of children’s products complies with all applicable safety rules.
The following are some factors that manufacturers and importers may consider when determining the frequency of testing ongoing production:
a. When there is high variability in test results
b. When there are measures that are close to the permissible numerical limit for quantitative tests
c. When there are new component part sets introduced into the manufacturing process
d. When there is a potential risk for serious injury or death resulting from the product’s noncompliance, among other factors
Toy Safety Directive (EU)
The Toy Safety Directive’s purpose is to reduce safety risks posed by children’s toys placed in the EU market. It applies to products that are designed or intended for use in play by children under the age of 14 years old.
The directive sets safety requirements for toys, such as mechanical properties, chemical properties, or flammability. Additionally, under the directive, there are harmonised standards (e.g. EN 71 standards) that, if complied with, give rise to a presumption of conformity with said safety requirements.
Testing frequency
Importers and manufacturers must put in place and hold on to technical documentation relating to the produced toy. Such documentation would contain information about the product including proof of compliance with the safety requirements of the directive.
There are certain factors that would necessitate subsequent testing as importers and manufacturers are obliged to:
a. To ensure that procedures are put in place for series production to remain in conformity, and take into account any changes in toy design or characteristics and changes in the harmonised standards by reference to which conformity of a toy is declared
b. Carry out sample testing of marketed toys when safety risks arise
Finally, in some cases, the conformity assessment procedure might require the involvement of a Notified Body
FCC 47 CFR Part 15 (US)
The FCC 47 CFR Part 15 – Radio Frequency Devices regulates the interference radiation generated by electronic products. The FCC aims for end devices to:
- Result in no harmful interference to other users
- Be capable of operating under the influence of other devices
Additionally, if your device is causing any type of unacceptable emissions, it may not be compliant with the regulations. This may affect the importer’s or manufacturer’s ability to place the device on the US market.
Testing frequency
According to our research, there are no explicit requirements for a periodic testing plan. However, when component or design changes are made or when new applicable standards are introduced, then you may need to go for subsequent testing.
The product should be tested pre-authorization. There are different authorization routes depending on how the device is classified under 47 CFR Part 15 which may even necessitate the involvement of an accredited lab (in the case of intentional radiators).
In general, testing should be done by a laboratory that contains the necessary measurement facilities to assess the product and should take place before the product enters mass production. New modifications to the product might necessarily require a new compliance test report.
However, importers and manufacturers may be requested to submit their products to an FCC lab any time after authorization. This is done to confirm that the products continue to apply the applicable standards.
Electromagnetic Compatibility Directive (EU)
The Electromagnetic Compatibility (EMC) Directive fulfills the purpose of limiting electromagnetic emissions from equipment to ensure that such equipment does not disturb radio and telecommunication, as well as other equipment.
Additionally, the EMC Directive governs the equipment’s immunity to interference and aims to ensure that such equipment is not disturbed by radio emissions.
The directive includes a list of harmonised standards. Following such standards provides the product with a presumption of conformity with the technical requirements of the directive.
Testing frequency
There are no explicit requirements to develop a periodic testing plan. However, any changes made to the apparatus design or characteristics and changes in the harmonised standards or in other technical specifications by reference to which conformity of apparatus is declared should be taken into account as it may require additional lab testing.
Conformity assessment
The manufacturer or importer might carry out one of the following compliance assessment procedures:
- Internal production control
- EU-type examination
Internal production control
Following the first method, the importer or manufacturer would have to perform an electromagnetic compatibility assessment, including relevant lab testing and include such reports in the technical documentation.
EU-type examination
As for the second method, a Notified Body is required. The Notified Body examines the technical documentation provided. When necessary, it may perform additional testing and proceed with the final evaluation.
21 CFR – Medical Devices (US)
The Food and Drug Administration (FDA) approves medical devices before they enter the US market. Medical devices are classified into three regulatory classes:
- Class I – Lowest risk and general control required
- Class II – Moderate risk and special control required
- Class II – High risk and special control required
Class I can be self-registered, but Class II medical devices require 510 (k) premarketing notification at least 90 days prior to the placement of the devices in the US market. As for Class III medical devices, the FDA requires that importers and manufacturers submit a premarket approval application before placing the device on the market.
Other than the above, there exist three more types of premarket submissions for other medical devices:
- Investigational Device Exemption (IDE)
- De Novo
- Humanitarian Devices Exemption (HDE)
Testing frequency
Periodic testing may be a requirement for some Class II and Class III devices. However, where there are changes in the design or components of the device or updates in applicable standards, subsequent testing may be necessary
Class I Devices
According to our research, a periodic testing plan is not needed. Although some Class I devices are exempt from Quality Management System (QMS) requirements, most devices would require the implementation of a QMS to meet the requirements contained in 21 CFR Part 820 which is the relevant regulation for medical devices in the US.
Class II and Class III Devices
For some Class II and all Class III devices, clinical studies would be required and importers and manufacturers should get pre-submission feedback from the FDA. For non-significant risk studies, they may be performed with the approval of an Institutional Review Board.
After completion of all the administrative requirements and the company along with the device(s) registration status is listed on the FDA website, you should be able to sell the device on the US market. However, if there are changes made to the medical device, then your authorization may expire.
Additionally, the FDA may impose post-approval requirements as a condition for the approval of the device. Such conditions may include the following:
a. Batch testing of the device
b. Continuing evaluation and periodic reporting on the safety, effectiveness, and reliability of the device for its intended use
Medical Devices Regulation (EU)
The Medical Devices Regulations (MDR) took effect on 26 May 2021 after a four-year transition period. The regulations changed the European legal framework for medical devices. Importers and manufacturers must comply with the regulation to place medical devices on the market.
The devices are classified depending on the grade of risk for the human body, intended use, or in terms of general safety.
There are three classes of devices:
a. Class I Devices
b. Class II Devices – which are split into two types: Class IIa and Class IIb
c. Class III Devices
Testing frequency
Periodic testing may apply depending on the classification of the product. For any device, manufacturers must ensure that they meet the general safety and performance requirements, including carrying out a clinical evaluation (see article 5(3), article 61, and Annex XIV of the directive).
For implantable devices and class III devices, it is compulsory to conduct a premarket clinical investigation unless exemptions apply.
Post-market surveillance
Manufacturers must update the clinical evaluation with clinically relevant information arising from the post-market clinical follow-up. The classification of the device would determine what needs to be prepared and whether it is done periodically:
a. For class I devices – the manufacturer must prepare and maintain a post-market surveillance report as per article 85 of the directive. It must be made available to competent authorities upon request
b. For class IIa, IIb and III devices – the manufacturer must prepare a periodic safety report as per article 86 of the directive. For class IIa devices, the report is updated at least every 2 years, and its is updated at least every year for class IIb and class III devices
Conformity assessment
The conformity assessment for Class I devices is usually carried out under the sole responsibility of the manufacturer. However, for higher categories, an appropriate level of involvement of a notified body is required, which might also include periodical audits.
Comparison Table
The following table summarizes information relating to lab testing frequency requirements of the regulations covered in this article.
Regulation | What is the product lab testing frequency? |
CPSIA (US) | a. Initial certification testing
b. Material change testing c. Periodic testing (depending on the ‘periodic testing’ plan, testing may occur once every year, every two years, or every three years) |
Toy Safety Directive (EU) | a. Toys must be tested at least once to ensure conformity with the requirements of the directive
b. Additional testing is dependent on a number of factors (e.g. new risks identified, changes made to the toy’s characteristics, and changes in harmonised standards) |
FCC Part 15 (US) | a. Devices must be tested at least once before production
b. A new test report may be necessary following modifications to the product |
EMC Directive (EU) | a. Devices must be tested at least once to ensure conformity with the requirements of the directive
b. Additional testing may be necessary upon modifications made to the equipment |
21 CFR – Medical Devices (US) | a. Depends on the risk classification of the device
b. Authorization may expire if modifications are made to the product c. There may be FDA post approval requirements for some Class II and Class III devices, including periodic testing |
Medical Devices Regulation (EU) | a. Depends on the risk classification of the device
b. Regardless all products must go through clinical evaluation, and include a plan which may contain more scheduled testing c. Excluding most Class I devices, auditing by a notified body is done periodically. Generally, the higher the risk classification the more interactions and audit plan is required |