Chemical, flammability, and safety lab testing is often required when importing and manufacturing clothing and other textiles in the United States. In this guide, we cover textiles testing costs, standards, compliance risks, and more.
Content Overview
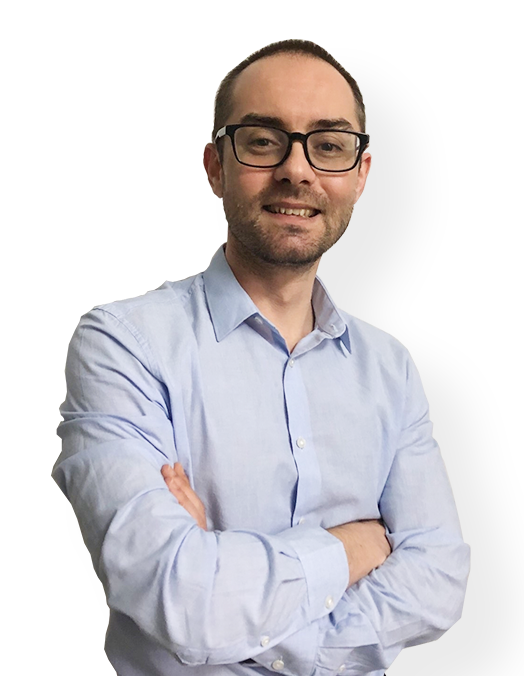
FREE CONSULTATION CALL (US, EU & UK)
- Request a free 30-minute call with Ivan Malloci to learn how we can help you with:
- Find product requirements
- Certification and labeling
- Lab testing
Is lab testing mandatory for clothing and textiles in the United States?
Whether lab testing is mandatory for apparel depends on the age group, fabric type, state, and other factors.
CPSIA lab testing
CPSIA covers all children’s products (12 years or younger) in the United States – including infants and children’s apparel. CPSIA covers the following:
- Chemicals and heavy metals
- Physical and mechanical properties (e.g. small parts)
- Flammability
CPSIA testing normally corresponds to CPSC rules and ASTM standards. Here are some examples:
- ASTM F963-17
- 16 CFR Part 1615, Standard for the Flammability of Children’s Sleepwear
- 16 CFR Part 1616, Standard for the Flammability of Children’s Sleepwear
- CPSIA Section 101 Children’s Products-Total Lead (Pb) Content
Third-party lab testing is mandatory, and the CPSC only accepts test reports issued by CPSC accepted labs.
Flammable Fabrics Act (FFA) lab testing
The FFA sets compliance requirements concerning fabric flammability. 16 CFR Part 1610 and 1611 covers flammability testing standards and lab testing methods for cotton, vinyl plastic film, and other fabrics.
The FFA testing process also corresponds to the rules outlined in the mentioned regulations.
- 16 CFR Part 1610 – Standard for the Flammability of Clothing Textiles
- 16 CFR Part 1611 – Standard for the Flammability of Vinyl Plastic Film
- 16 CFR Part 1615 – Standard for the Flammability of Children’s Sleepwear: Sizes 0 Through 6X
- 16 CFR Part 1616 – Standard for the Flammability of Children’s Sleepwear: Sizes 7 Through 14
California Proposition 65 lab testing
California Proposition 65 restricts heavy metals and chemicals in consumer products sold in California, including garments. Lab testing is required in order to verify if the product contains restricted substances above the set limits.
Note: There are also other state regulations in the United States that apply to garments. This guide only covers a few examples of lab testing compliance requirements in the United States.
What types of tests may be necessary?
Here’s an overview of different types of lab tests that can be applied to garments:
Fabrics testing
Fabrics can be tested according to chemicals and heavy metals content, and flammability. Fabrics that contain excessive amounts (e.g. above the set limits) of lead, cadmium, and other restricted substances are non-compliant.
Garment accessories testing
Buttons, zippers, velcro, and other garment accessories can also be tested for heavy metals and chemical content.
Mechanical & Physical Properties testing
Mechanical and physical properties testing are mainly relevant when testing children’s clothing. Such testing includes small parts testing, sharp points testing, and general assessments of the safety of the overall design.
How much does US clothing and textiles testing cost?
The lab testing costs depend on the following factors:
- Age group (e.g. 1 to 3, 12+)
- Fabric type (e.g. polyester and cotton)
- Parts (e.g. zippers and buttons)
- Number of colors
Lab testing costs multiply based on the number of tests. As such, the lab testing costs increase for every material type, color, and part that goes into the creation of your product.
As mentioned, additional lab testing is necessary for children’s clothing.
Cost Examples
- Fabric (chemicals and heavy metals): $80 – 250 per fabric and color
- Zippers (chemicals and heavy metals): $50 – 200 per part
- Fabric (flammability): $50 – 200 per fabric
- Physical and mechanical: $200 – 800 per item
Can we lower the lab testing costs?
Here are some ways you can reduce your testing costs:
1. Avoid fabrics covered by the FFA
2. Avoid children’s clothing
3. Limit the number of different materials, colors, buttons, and zippers
4. When possible, only test materials once
Does the lab test have to take place in the United States?
In most cases, no. However, it is sometimes mandatory to use certain ‘approved’ labs. For example, children’s products must be tested by a CPSC accepted lab.
When should we send the apparel for lab testing?
Garment testing can either take place before or after production. This table explains the pros and cons:
Pros | Cons | |
Pre-Production (Sample) Testing | + Verify physical/mechanical compliance before mass production | – Batch testing is sometimes mandatory (sample testing not accepted) – Chemicals and heavy metals testing may not be an option as materials may not match |
Post-Production (Batch) Testing | + Batch testing is sometimes mandatory (sample testing not accepted) + The final product is verified as compliant (if it passes) |
– Failed testing may force you to discard the entire product batch |
Both | + Very low risk of producing and shipping a non-compliant product | – Expensive |
How do I know which garment testing standards apply?
My recommendation is to contact a lab testing company, such as QIMA or Intertek, and request a lab test quotation. They normally list all applicable tests as part of the lab testing quotation.
The testing company needs the following information to provide an accurate testing quote:
- Product name
- Bill of materials
- Age group
You should also clarify which states your apparel will be sold in.
Can we obtain a garment lab test report from our supplier?
No, manufacturers don’t have access to lab test reports for all fabrics, zippers, and other parts. Most garment manufacturers source materials as needed – and the materials suppliers in turn tend to lack test reports.
It’s therefore necessary to arrange lab testing when importing and selling clothing and other textile products in the United States.
What happens if our garments or textiles fail testing?
How to deal with testing failure depends entirely on the cause. The table below includes some examples:
Cause | Solution |
Fabrics contain excessive amounts of chemicals and heavy metals | None (fabric cannot be replaced – product must be discarded) |
Buttons and zippers excessive heavy metals | Rework the produced pieces by replacing the buttons and zippers |
Small parts or strangulation hazard | Rework the design before you enter mass production |
Is it common that textile fabrics and garment accessories fail to test?
Here are some examples of apparel recalls listed on the CPSC website:
- JCPenney Recalls Girls Puffer Jackets Due to Entanglement Hazard (Link)
- H.I.S. Recalls Girl’s Clothing Sets Due to Violation of Federal Lead Content Ban (Link)
- LIVLY Recalls Children’s Sleepwear Due to Violation of Federal Flammability Standard (Link)
While a recall is not necessarily the result of testing failure, these examples demonstrate some of the risks involved.
A personal observation, however, is that the risk of substance testing is fairly low when it comes to fabrics, but higher for metal parts such as buttons and zippers.
When it comes to physical and mechanical testing failure it comes down to ensuring that the product is designed for compliance before entering production.
What can happen if we don’t have a lab test report?
Failing to provide a lab test report can result in fines, forced recalls, and Amazon removing your product listings. Keep in mind that lab testing is often mandatory when importing and selling clothing and textile products in the United States.
Hi. i am a drycleaner owner. I need a test for my customer. I have to know it is from manufacture or one of my chemical. how much you will charge?