Children’s clothing sold in the United States is subject to various safety standards, chemical and heavy metal restrictions, labeling, testing, and certification requirements.
In this guide, we cover some of the most important regulations and requirements, including CPSIA, ASTM standards, tracking labels, 16 CFR Part 1120, flammability requirements, and more.
Note that some regulations and standards mentioned in this guide are not exclusively applicable to children’s products but to consumer products and apparel in general.
Content Overview
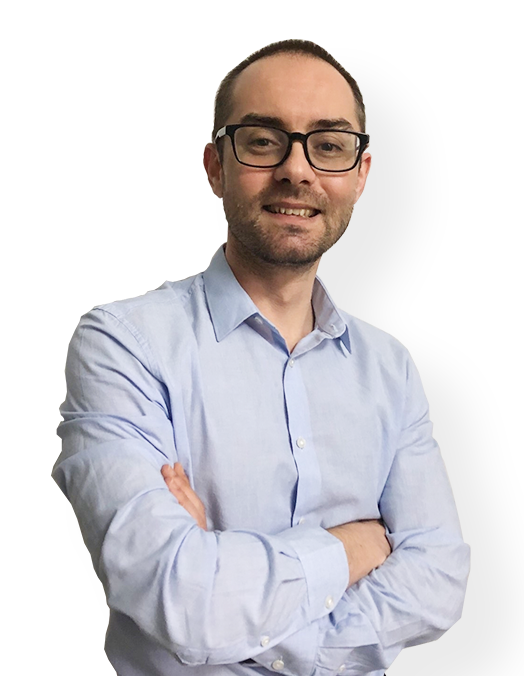
FREE CONSULTATION CALL (US, EU & UK)
- Request a free 30-minute call with Ivan Malloci to learn how we can help you with:
- Find product requirements
- Certification and labeling
- Lab testing
Consumer Product Safety Improvement Act (CPSIA)
CPSIA regulates children’s products, including children’s clothing sold in the United States. The US Consumer Product Safety Commission (CPSC) defines children’s products as any “consumer products designed or intended primarily for children 12 years of age or younger”.
Safety standards
The CPSIA requires that children’s clothing must comply with relevant standards (e.g. ASTM standards), substance restrictions, and other rules. Some standards, rules, and substance restrictions only apply to specific types of children’s products, while others apply broadly to all children’s products.
Examples
a. 16 CFR Part 1303 – Ban of Lead-Containing Paint and Certain Consumer Products Bearing Lead-Containing Paint
b. 16 CFR Part 1615 – Standard for the Flammability of Children’s Sleepwear: Sizes 0 through 6X
Children’s Product Certificate (CPC)
Importers and manufacturers must issue a CPC for their products, to certify that the children’s clothing complies with applicable requirements (e.g. substance restrictions). The CPC is a self-issued document with information such as product name, supplier information, relevant standards, and testing result.
Summary
1. Product name and description
2. List of applied standards
3. Importer information (name, address, e-mail address, phone number)
4. Contact information of the person with access to the test report (name, address, e-mail address, phone number)
5. Manufacturing location (city, province, country) and date (month, year)
6. Testing date (month, year) and location (city, province, country)
7. CPSC accepted third-party lab testing (company, contact person, address, phone, email)
Learn more
You can read this guide for more information about CPC when importing children’s clothing.
CPSIA Tracking Label
You must prepare a CPSIA tracking label for your children’s clothing. Here is an overview of the required label information:
- Company name
- Company information
- Production location
- Production date
- Batch number
Label file
The supplier expects the buyer to provide a ready-made label file. In addition to the tracking label, you must also provide the following information:
- Print position
- Dimensions
- Colors
- Print type
Learn more
You can read this guide for more information about the CPSIA tracking label.
CPSIA Testing
Third-party lab testing for children’s clothing is mandatory to verify that your children’s apparel or babywear is compliant with applicable standards. You can only carry out third-party lab testing via CPSC-accepted testing companies.
Some suppliers might provide a CPSIA test report for children’s products that are similar to the ones you want to import. However, a test report is only valid for the very same products that you are importing to the United States. That means you must collect the sample from the production batch and submit it to the laboratory for testing.
List CPSC accepted testing companies
- Eurofins
- CMA Testing
- UL
- SGS
- QIMA
Click here for a more comprehensive list of CPSC-approved testing companies.
CPSIA testing costs
The cost depends on applicable standards, materials, and colors. In general, it starts at around $300 per children’s clothing style. That said, this cost increases significantly if your children’s clothing is made of several fabrics, colors, buttons, zippers, velcro, and other material.
As such, the best way to keep costs down is by reducing the number of different fabrics, colors, and components. For example, you can save on testing fees by using the same fabrics, colors, zippers, and buttons on many different products.
Substantial Product Hazard List (16 CFR Part 1120) – Drawstrings in Children’s Upper Outerwear
16 CFR Part 1120 – Substantial Product Hazard List states that children’s upper outerwear with one or more drawstrings is deemed to be a substantial product hazard, and is subjected to the requirements of ASTM F1816-97 standard.
The standard prohibits drawstrings on the hood and neck of children’s upper outerwear in sizes 2T to 12 (or equivalent) because they present a strangulation hazard.
Also, any drawstring for children’s upper outerwear in sizes 2T to 16 at the waist or bottom of the product should be stitched in such a way to prevent it from being pulled through its channel.
Specifically, the drawstrings on the waist and bottom of children’s upper outerwear in sizes 2T to 16 could be hazardous if the drawstring:
a. Exceeds 3 inches outside its channel; and
b. Has any toggles, knots, or other attachments on its ends.
Flammable Fabrics Act
The Flammable Fabrics Act (FFA) regulates the manufacture and import of highly flammable clothing and other textiles. As well as covering adult clothing, the FFA also covers children’s products.
Product scope
The CPSC has issued mandatory flammability standards under the FFA, for fabrics used in apparel such as:
- Children’s sleepwear
- Clothing textiles
- Vinyl plastic film (used in clothing)
16 CFR Part 1610 – Standard for the Flammability of Clothing Textiles
The purpose of 16 CFR Part 1610 is to reduce the danger of injury and loss of life due to flammable clothing. It prohibits importers and manufacturers from using any dangerously flammable textiles to manufacture clothing (including those for children). 16 CFR Part 1610 provides, on a national basis, standard methods of testing and rating on textiles’ flammability.
Product scope
16 CFR Part 1610 covers clothing textiles, excluding Class 1 fabrics, as those are deemed safe to use in clothing because these textiles demonstrate normal flammability behavior. This is how Class 1 fabrics are defined:
a. Plain surface fabrics (all fibers) weighing a minimum of 2.6 ounces per square yard
b. Fabrics (regardless of surface and weight) that are composed of acrylic, modacrylic, nylon, olefin, polyester, and/or wool
Additionally, the standard exempts some type of products, such as:
a. Hats – provided they don’t cover the face, neck, or shoulders of individuals when worn
b. Glove – provided they don’t exceed 14 inches in length and aren’t an integral part of another garment
c. Footwear – provided it’s not made of hosiery and not an important part of another garment
Classification
The standard defines three classes of flammability:
- Class 1, Normal flammability
- Class 2, Intermediate flammability
- Class 3, Rapid and intense burning
Plain surface textile fabrics can be classified as:
a. “Class 1, Normal flammability”, if said fabrics take more than 3.5 seconds to burn
b. “Class 3, rapid and intense burning”, if the flames on the fabric spread in less than 3.5 seconds
Raised surface textile fabric can be classified as:
a. “Class 1, Normal flammability”, if said textiles take more than 7 seconds to burn
b. “Class 2, Intermediate flammability”, if the fabric burns within 4 through 7 seconds
c. “Class 3, Rapid and intense burning”, if the flames take less than 4 seconds to spread
Testing requirements
16 CFR Part 1610 provides methods of testing the flammability of textiles and forbids the use of textile fabrics that burns too fast. Specifically, Class 3 textiles should never be used for clothing as they:
- Exhibit rapid and intense burning, and
- Are dangerously flammable
According to the standard, all textile fabrics are required to undergo a first round of testing in their original state, be refurbished, before being tested again. The preliminary tests should be carried out on the fabrics in a state ready for use in wearing apparel.
Tested textiles should be refurbished by being dry-cleaned and laundered using the AATCC Test Method, before a retest.
16 CFR Part 1611 – Standard for the Flammability of Vinyl Plastic Film
16 CFR Part 1611 is a codification of a previous flammability standard for vinyl plastic film. The standard became mandatory through the FFA and remains in effect.
The purpose of 16 CFR Part 1611 is to set minimum standards for the flammability of vinyl plastic film, including materials used in wearing apparel.
Product scope
16 CFR 1611 covers nonrigid and unsupported vinyl plastic, including the following types of material:
- Transparent
- Translucent
- Opaque
- Plain
- Embossed
- Molded
- Otherwise surface treated
Testing requirements
16 CFR Part 1611 requires the rate of burning to not exceed 1.2 inches per second when the material is tested with the flammability tester per the method outlined in the standard.
The standard also notes that if any covered article of wearing apparel or fabric has been tested accordingly to be so dangerously flammable when worn by individuals, those articles of clothing should not be handled or marketed.
16 CFR Part 1615 and 1616 – Standard for the Flammability of Children’s Sleepwear
Both 16 CFR Part 1615 and 16 CFR Part 1616 apply to the flammability of children’s sleepwear, which includes apparel intended to be primarily worn for sleeping or sleep-related activities. Such apparel includes:
- Nightgowns
- Pajamas
- Robes
While infant garments (garments sized nine months and smaller) are exempted from 16 CFR Part 1615, items such as diapers, underwear, and tight-fitting garments are exempt from both standards.
Product scope
16 CFR Part 1615
This standard covers the provision of a test method to determine the flammability of children’s sleepwear sizes 0 through 6X, are.
16 CFR Part 1616
The 16 CFR Part 1616 standard covers the provision of a test method to determine the flammability of children’s sleepwear sizes 7 through 14, are.
Requirements
16 CFR Part 1615 and 1616 require samples to be vertically suspended and subject to standard burning procedures along the garment’s bottom edge for a specific time under controlled conditions.
Both standards require children’s sleepwear items to be labeled with precautionary instructions protecting the garments from treatments or agents known to cause deterioration of their flame resistance.
If the relevant garment has been tested after a single wash and dry session, it should be labeled with instructions to wash before wearing. Such labels should be permanent and comply with the CPSC’s rules and regulations.
ASTM D1230 – Standard Test Method for Flammability of Apparel Textiles
ASTM D1230 is a standard test method that covers the evaluation of how flammable textile and apparel fabrics are (other than children’s sleepwear). The test method described in ASTM D1230 measures and describes how assemblies, materials, or products respond to heat and flame under controlled conditions.
This method does not by itself incorporate every factor required for assessing the assemblies, materials, or products for fire hazards or fire risks under actual fire conditions.
Textile, Wool and Fur Acts and Rules
The Textile, Wool, and Fur Acts and Rules require importers and manufacturers to label their products (including children’s clothing products) with information that includes
- The name of the importer or manufacturer, or Registered Identification Number (RN)
- Fiber/fur content
- The product’s country of origin
Product scope
The Textile, Wool and Fur Acts and Rules cover most clothing (including those worn by children) and textile products, which include all fibers, yarns, and fabrics, such as:
- Clothing (except hats and shoes)
- Scarves
- Bedding
Bedding products covered by the Acts and Rules include:
- Sheets
- Blankets
- Pillows
- Bedspreads
Labeling requirements
Below we list the labeling requirements for different products.
Textile and wool products
Importers, manufacturers, and sellers who offer to sell, distribute, or advertise products covered by the Textile and Wool Acts are required to comply with the labeling requirements, which include:
- Identity of business or manufacturer, or RN
- Fiber content
- Country of origin
Fur products
Fur products have unique labeling requirements. The FTC requires fur products to bear labels disclosing the following information:
a. The animal name
b. The name or RN of the importer, manufacturer, or distributor
c. The country of origin for imported fur
d. If the fur is artificially colored, bleached, dyed, or pointed
e. If the fur product is composed in whole or substantial part of other pieces
f. If the fur is damaged or used
g. The textile or wool content of any part of the product.
Care Labeling of Textile Wearing Apparel & Certain Piece Goods
16 CFR Part 423 is a regulation that outlines how textile wearing apparel and certain piece of goods should include labels with care information.
Product scope
Regulation 16 CFR Part 423 covers importers and manufacturers of textile-wearing apparel (including children’s clothing products) and certain piece goods. The regulation applies to any organization or person directing or controlling the importation or manufacture of covered products.
Labeling requirements
This regulation requires importers and manufacturers of wearing apparel and some other textile products to provide care instructions through the use of care labels. Instructions might include:
- Washing instructions
- Drying instructions
- Ironing instructions
- Bleaching instructions
- Warning instructions
Importers and manufacturers are required to attach easily visible care labels to products offered for sale to consumers. If the label is in any way obscured on the product, the care information (stating the regular care for ordinary use of the product) should be clearly labeled on either the outside of the package or on a hang tag fastened to the product.
Importers and manufacturers should provide care information clearly and conspicuously on the product.
You can find more information here.
California Proposition 65
California Proposition 65 regulates more than 800 toxic substances in all products sold in California, as they are deemed to cause cancer, congenital disabilities, or other reproductive harm. California Proposition 65 also covers children’s clothing.
Examples of restricted substances
- Lead
- Cadmium
- Formamide
- Hydrazine
Warning Labeling
Otherwise, if you are not sure that your children’s apparel doesn’t contain an excessive amount of restricted substances, you must attach a warning label to the product or its packaging.
You can avoid the warning label by verifying California Proposition 65 compliance through third-party testing.
California Proposition 65 lab testing
The restricted substances list is updated on a non-regular basis, and most children’s clothing manufacturers in Asia cannot provide California Proposition 65 test reports.
Therefore, third-party lab testing is often the only way to verify if your product complies with the proposition’s substance restrictions. We recommend that you book a lab test for your children’s clothing products before shipping them to the United States.
Testing costs
In general, the testing cost starts at $200, and it can increase depending on the number of styles, materials, components (e.g. buttons and zippers), and colors.
Testing companies
Click here to see a list of California Proposition 65 lab testing companies.
Country of Origin
The country of origin marking is mandatory for most products sold in the United States. This requirement also covers children’s clothing. The country of origin marking must be permanently affixed to the product and its packaging.
Examples
- Made in Japan
- Made in China
- Made in Vietnam
- Made in Bangladesh
- Made in India
- Made in Germany
- Made in France
Label file
You can’t expect your manufacturer to create a country of origin label for your product. You must create the label files in .ai or .eps formats, then submit them to your manufacturer before mass production.
Amazon Children’s Clothing Requirements
You will need to obtain approval from Amazon before you start selling children’s clothing on their platform. As such, your products must comply with mandatory standards, regulations, certifications, and labeling requirements. Sellers also need to provide the CPC, ASTM test report, and other relevant documents before they can start selling.
You should read the relevant product category requirements carefully in the Amazon Seller Central before you import and sell children’s clothing on Amazon.com.
How does Amazon check product compliance?
Amazon might request several documents, including lab test reports, CPC, product photos, or invoices of your products at any time.
Amazon has the right to review your children’s clothing products for compliance checking purposes. They often reject sellers that cannot provide the required documents.
What can happen if we sell non-compliant children’s clothing on Amazon?
Amazon can remove your product listing from Amazon.com and suspend your account if needed. Note that Amazon often limits its actions to specific SKUs, even though they can also decide to suspend your whole account.
Does each lot of fabric used in connection with the manufacture of newborn apparel products require the necessary testing? Once having been successfully tested if you secure the product from the same resource do subsequent lots need to be tested?
Hello,
CPSIA requires that you implement a periodic testing plan – but I don’t think there is a set testing frequency.
When there is a change to the materials or colors, or if a standard is updated, then testing is required.
The testing frequency also depends on how much control you have over the manufacturing process:
“An importer, or a manufacturer who exercises little or no control over the manufacturing process, will need to exercise due care to ensure that it has the knowledge necessary to make appropriate decisions about the frequency of testing necessary for continued production and additional batches and lots of products.”
It ultimately comes down to risk management.
What if I am making the Children’s Wear – ages 2-12 IN the UNITED States? I am Using OEKO TEX Fabrics, and making in NYC. Just Sportswear, no Sleep. But we are using GrossGrain ties and Buttons and Zippers. Where can I find the Requirements for these?
What about zipper regulation? Did I miss it? I recently learned there are rules about zippers for baby pajamas
We are directly a manufacturer of children’s pajamas and may qualify for exemption from certain tests as a Small Batch Manufacturers. To your knowledge does Amazon accept such exemptions?
I have received emails from sellers stating that Amazon did reject them even though they qualified as Small Batch Manufacturers. I don’t know if this is Amazon policy or a misunderstanding from their compliance team.
This was a detailed yet crisp list of regulations and certifications to be followed. For organic clothes you need more certifications, right?
Hi Lana,
I suggest you read this article as it covers organic cotton certification: https://www.chinaimportal.com/blog/importing-gots-organic-cotton-textiles-from-china/